Technology
HONEYWELL INTRODUCES NEW TECHNOLOGY TO PRODUCE KEY FEEDSTOCK FOR PLASTICS
BIO-NPHTHA WITH REDUCED CO2 FOOTPRINT
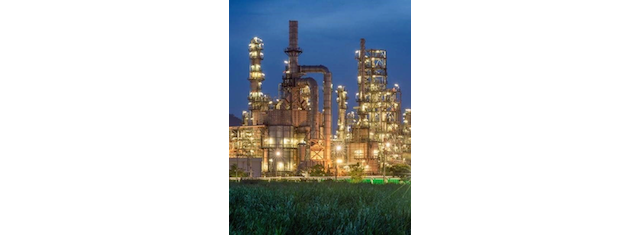
HONEYWELL * (Source: Honeywell)
USPA NEWS -
Honeywell announced on February 9, that it has introduced a new solution for producing renewable naphtha for petrochemical production using the commercially proven Honeywell UOP Ecofiningâ„¢ technology. The new pathway can produce high yield of naphtha from sustainable feedstocks like used cooking oil and animal fats.
Honeywell announced on February 9, that it has introduced a new solution for producing renewable naphtha for petrochemical production using the commercially proven Honeywell UOP Ecofiningâ„¢ technology. The new pathway can produce high yield of naphtha from sustainable feedstocks like used cooking oil and animal fats.
Naphtha is a valuable petrochemical feedstock used in the production of plastics, specifically olefins that are building blocks for other chemicals and aromatics that are used to produce polyester and other packaging materials. Naphtha is traditionally derived from crude oil and natural gas condensates but can now be produced from renewable feedstocks. Renewable naphtha from sustainable feeds such as used cooking oil has a 50%-80% lower greenhouse gas footprint compared to petroleum feeds, depending on the feedstock.
Naphtha is a valuable petrochemical feedstock used in the production of plastics, specifically olefins that are building blocks for other chemicals and aromatics that are used to produce polyester and other packaging materials. Naphtha is traditionally derived from crude oil and natural gas condensates but can now be produced from renewable feedstocks. Renewable naphtha from sustainable feeds such as used cooking oil has a 50%-80% lower greenhouse gas footprint compared to petroleum feeds, depending on the feedstock.
Prior to the introduction of renewable naphtha solution, the UOP Ecofining technology has been used to produce predominantly Honeywell Green Diesel and Honeywell Green Jet fuel, with small amounts of bio-naphtha being produced as a secondary product. The same Ecofining technology can be adapted to produce high yields of renewable naphtha as its predominant product, reflecting the versatility of the Ecofining design and ability to produce a range of products based on market needs.
"We are actively engaged with customers to drive new technology adoption, as renewable petrochemical feedstocks have grown in interest as consumers prefer more bio-based products," said Ben Owens, vice president and general manager, Honeywell Sustainable Technology Solutions. "We see renewable naphtha produced from the UOP Ecofining process as a proven solution available today to help petrochemical producers reduce the carbon footprint of their products compared to using petroleum-based feeds."
For additional methods of decarbonization, the UOP Ecofining process for renewable naphtha can be combined with renewable hydrogen supply and CO2 capture and sequestration through the Honeywell H2 Solutions portfolio. For example, for an Ecofining unit with renewable hydrogen and CO2 capture processing 10,000 barrels per day of sustainable oil feedstock such as used cooking oil, renewable naphtha can deliver more than 1 million metric tons of CO2 emission reductions annually compared to petroleum naphtha.
Customers choose Honeywell UOP for production of renewable fuels due to our proven commercial experience and high product yields. The renewable naphtha process pathway is based on more than 20 years of combined operating experience of the Ecofining technology.
Honeywell UOP jointly developed the Ecofining process with Eni SpA. It converts non-edible vegetable oils and animal fats to Honeywell Green Diesel, which offers improved performance over biodiesel and petroleum-based diesel. The Ecofining process produces diesel with a cetane value of 80, substantially higher than the 40-to-60 cetane diesel commonly used in diesel engines today. As a result, this higher-cetane diesel fuel provides better engine performance and can be blended with cheaper low-cetane diesel to meet transportation fuel standards.
Honeywell UOP jointly developed the Ecofining process with Eni SpA. It converts non-edible vegetable oils and animal fats to Honeywell Green Diesel, which offers improved performance over biodiesel and petroleum-based diesel. The Ecofining process produces diesel with a cetane value of 80, substantially higher than the 40-to-60 cetane diesel commonly used in diesel engines today. As a result, this higher-cetane diesel fuel provides better engine performance and can be blended with cheaper low-cetane diesel to meet transportation fuel standards.
The UOP Ecofining process is used in most 100%-biofeed units producing renewable diesel -- and all of the licensed renewable jet fuel production -- in the world today. UOP currently has licensed 23 Ecofining units in eleven countries around the world, processing 12 different types of renewable feedstocks
* Photo cover: HONEYWELL introduces New Technology to produce Key Feedstock for plastics
Source: Honeywell
Ruby BIRD
http://www.portfolio.uspa24.com/
Yasmina BEDDOU
http://www.yasmina-beddou.uspa24.com/
* Photo cover: HONEYWELL introduces New Technology to produce Key Feedstock for plastics
Source: Honeywell
Ruby BIRD
http://www.portfolio.uspa24.com/
Yasmina BEDDOU
http://www.yasmina-beddou.uspa24.com/
Ruby Bird Yasmina Beddou Co2 Footprint Honeywell New Technology Key Feedstock Plastics Bio Naphtha Honeywell Uop Ecofining
Liability for this article lies with the author, who also holds the copyright. Editorial content from USPA may be quoted on other websites as long as the quote comprises no more than 5% of the entire text, is marked as such and the source is named (via hyperlink).